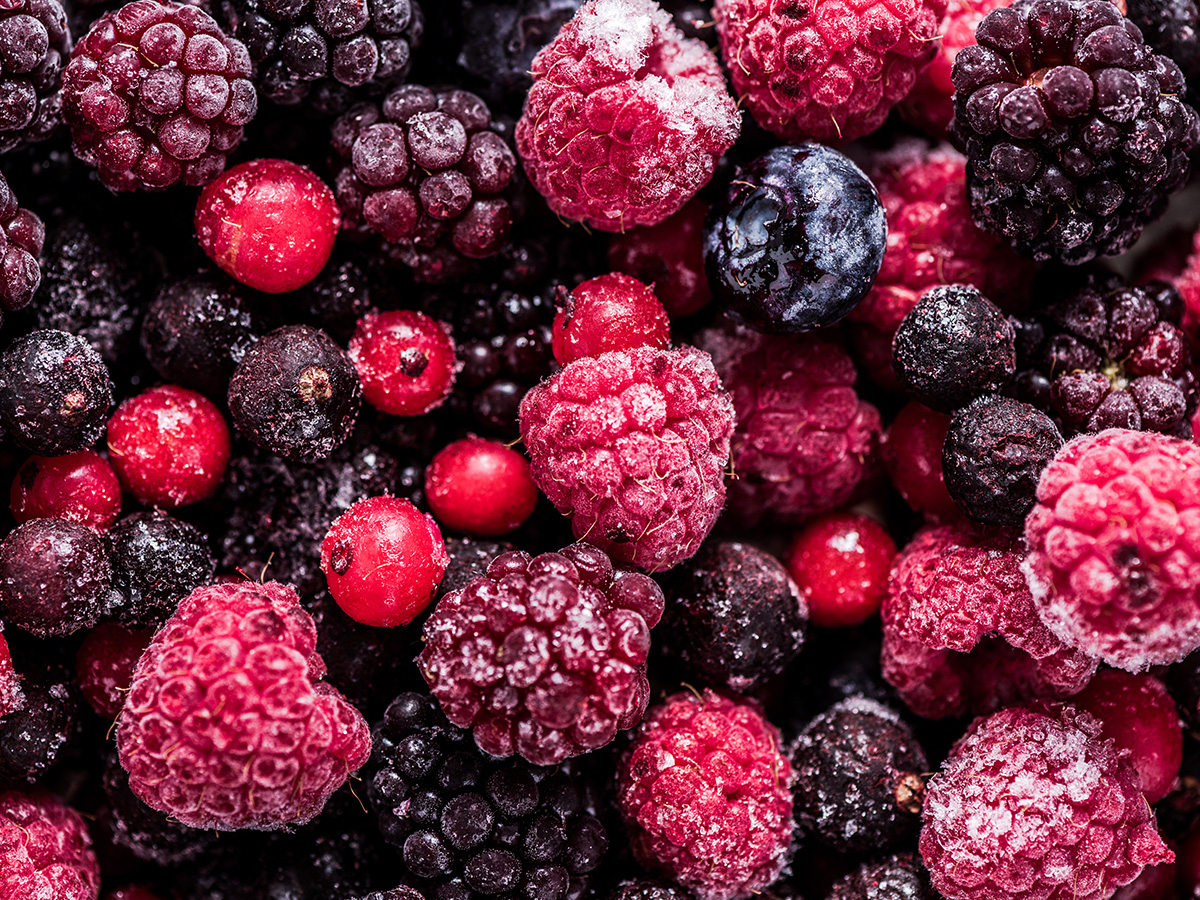
How to Overcome Challenges in Sustainable Packaging Production
Maybe you want to make the leap into producing recyclable packaging and are moving to a mono-material film. Or maybe you’ve already tried a mono-material film structure and experienced challenges running it on production machines, getting consistent sealing, or maintaining package integrity. Regardless, making the move from multi-material legacy films to mono-materials like polyethylene can feel like a momentous task. You have barrier properties to consider, ideal sealing temperatures to achieve, and an attractive package to produce.
So, how do you align the basic requirements of a package and functionality with sustainable formats?
Define What “Sustainability” Means for Your Packaging
As consumers call for a moratorium on single-use plastics and conflate sustainability with recyclability, recyclability is the ultimate goal for many brands. However, as we currently lack the infrastructure and consumer education to fully support recycling, you’ll also want to consider other facets of sustainability, in particular, how your package can support circularity. Whether it’s switching to flexible packaging for source reduction or following through on educating your consumer about the recyclability or compostability of your package, zeroing in on a goal will help you funnel your resources into the right places.
Take Advantage of Packaging Innovations
Packaging Equipment
Thanks to new developments in packaging materials and equipment, it’s now easier to produce a sustainable package that includes all of the necessary segments working in concert with each another. The process is now more forgiving than in the past, meaning fewer inefficiencies or quality control issues. For example, newer packaging equipment can now optimize converting and help maintain consistent sealing temperatures more effectively than earlier machines could with mono-materials.
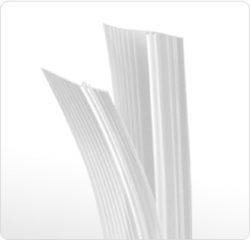
The 8000 Series is a line of sustainable closures for flexible packaging targeting circularity and waste elimination. Each closure is compatible with emerging film and manufacturing technologies while still delivering the ideal consumer experience for reclosable pouches.
New Films (Machine-Direction Oriented Polyethylene and Biaxally-Oriented Polyethylene)
There have also been developments to packaging films, such as machine-direction oriented polyethylene (MDO), which can give the package more integrity than traditional polyethylene, provide a slightly larger heat differential, and provide a glossier cosmetic effect. Biaxally-oriented polyethylene (BOPE) is another contender for getting packagers closer to what we can do with the legacy materials and films.
Soft Seal® Closures
New closure designs can also help mitigate some of the concerns around sealing and sustainability. Packaging manufacturers now have access to fully recyclable and compostable zippers or sliders optimized for recyclable films, such as those in the Fresh-Lock® 8000 series, which require less time, temperature, and energy to crush. That means packagers can add value to the package without worrying about sacrificing package integrity or sustainability.
Collaborate with Packaging Suppliers
“Packaging is going through a renaissance, and in order to thrive as a product marketer, especially one that markets to the consumer, you’ll need to show sustainable practices to maintain your place in the market or continue to grow. Consumer groups are looking into sustainability more closely and will begin to support those companies that are sustainable and surrender support to those who are not. However, when it comes to sustainability in packaging, it isn’t about just one part of the package. That means producing sustainable packaging takes the expertise of everyone working on that package.” –Todd Meussling, Senior Manager Market Development for Fresh-Lock® Closures
When you set out to design a sustainable package, it’s easy to focus on one supplier without having a larger conversation with others who play a role in the package’s development. However, the most successful and innovative projects come from a collaboration throughout the supply chain, whether that means connecting with the OEM or even your supplier’s supplier. Essentially, you’ll want to treat each party as an asset or a partner in producing the package, as each facet (whether films, closures, or something else) presents its own challenge. The suppliers of each component will be best suited to speak to the material’s unique capabilities, but partnership between everyone who has a part in producing the package is what allows for innovation.
Collaboration in Action: Producing a Recyclable, Reclosable Flexible Pouch
As part of the team that produced Bear Naked® Granola’s fully recyclable pouch, we witnessed the power of collaboration ourselves. The Fresh-Lock® (zipper) team worked with Berry Global (film supplier), Dow (barriers and sealant), and ColorMasters (ink, printing, and finish) to create a recycle ready, resealable stand-up pouch that was approved by the Sustainable Packaging Coalition (SPC). The new pouch is not only sustainable and convenient for consumers; it also has benefits for packaging manufacturers. It runs at faster machine speeds and lower sealing temperatures, and it has improved barrier requirements for enhanced shelf life. All of these features would not have been possible without the close collaboration between suppliers. Read more of the behind-the-scenes story.
Winner of 2020 FPA Silver Award in Sustainability
“What made the Bear Naked project run so well was the fact that all suppliers in the supply chain shared in the process. Each supplier voiced their concerns, where they needed help, and what they could offer that could help one of the other suppliers. The project wouldn’t have been nearly as successful if the collaboration hadn’t been there.” –Todd Meussling
Start the Conversation
It’s never too early to start collaborating with your suppliers on your next project. If you want to learn more about the Bear Naked® project or adding recycle-ready closures to your packaging, connect with the Fresh-Lock team today or follow us on the blog for more sustainability insights!